Certified Manager of Quality/Organizational Excellence (CMQ-OE) Interview Questions
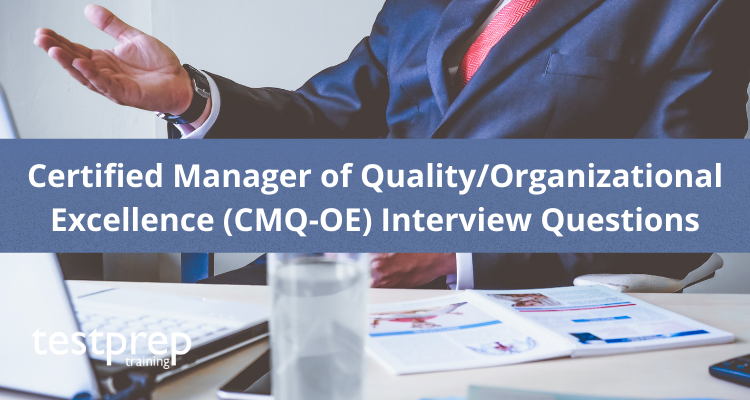
The Certified Manager of Quality/Organizational Excellence – CMQ-OE – ASQ exam assists the candidate in achieving the title of Certified Manager of Quality/Organizational Excellence. ASQ is in charge of administering the exam. In many industries, ASQ certification is regarded as a mark of quality excellence. Obtaining certification as a Manager of Quality/Organizational Excellence validates your dedication to quality and the positive impact it will have on your organization.
Quality management is an important function that is practiced by all industries, whether they are manufacturing or providing services. As a Quality Manager, you must ensure that the quality of an organization’s products, services, or processes is properly maintained on a regular basis in order to meet the customer’s requirements, which increases the organization’s efficiency. If you want to prepare for the big job interview, read through the Quality Management job interview questions and answers.
1. What is the distinction between I.S.O and C.M.M levels?
The CMM is a method of communicating capabilities. CMM is a very specific way of categorizing a company’s software development methods.
The ISO is a method of communicating the process. ISO-procedures describe a (possibly) definite development and process, but they provide no indication of the likely quality of the designs or whether multiple software efforts are likely to produce software of comparable quality.
2. What are the advantages of using a quality management system?
- Internal quality enhancement (reduction in scrap, rework and non-conformities in the shop)
- External quality enhancement (customer satisfaction, claims of non-conforming products, returned products, warranty claims, penalty claims etc)
- Increased production dependability (number of break downs, percentage down time etc)
- Enhancement of Time Performance (on-time delivery, time to market etc)
- Cost-cutting for low-quality products (external non-conformities, scrap, rework etc)
3. What exactly is a quality management plan (qmp)?
A QMP is a formal plan that documents an entity’s management system for the upcoming environmental work. The QMP is an “umbrella” document that describes the organization’s quality system in terms of organizational structure, functional responsibilities of management and staff, lines of authority, and required interfaces with those who plan, implement, and assess all environmentally related activities.
4. Define Quality Assurance.
- Firstly, It is an Assurance activity that focuses on the standards and procedures that must be followed when developing an application.
- It is a preventive action taken before hand to ensure that the product that is developed is defect free. It is a systematic action required to provide sufficient confidence that a product or service will satisfy the given quality requirements.
5. What do you understand by Quality Control?
It is a Corrective Action Inspection if the developed application adheres to the standards and procedures as outlined in the checklists.
6. What would you do to introduce the concept of tqm in the region where there is no quality management?
In the absence of Quality processes, we would encourage them to identify and document each and every task for each process. Then, we’d advise them to define and document what they can do to reduce human or machine errors. We would encourage them to identify wastes such as material or time wasters and develop processes to reduce these wastes. I would instruct them to record and document each discovery, as well as to strive to improve each process.
7. Which procedures must be followed when putting in place a quality management system?
When establishing and implementing quality management systems, the Deming cycle (PDCA) is recommended.
8. What are the quality fundamentals?
There are eight quality principles:
- Firstly, Customer focus
- Secondly, Leadership,
- Involvement of people,
- process approach,
- System approach to management
- Continual improvement
- Factual approach to decision making,
- Mutually beneficial supplier relationship
9. What are the six required quality procedures?
- Firstly, Document management
- Secondly, Record-keeping supervision
- Next, Production equipment, tools, and CNC programmes are all under your control.
- Further, Nonconforming Product Control
- Preventive Measures
- Corrective Measures
10. What exactly are quality improvement activities?
Quality improvement activities provide an opportunity for the practice’s GPs and staff to work as a team to consider quality improvement.
11. What exactly is risk?
- Risk can be defined as anything that causes a failure, defect, or error in an application or process.
- We can reduce risk by incorporating a proper risk matrix into the process. The Risk Matrix displays the controls within application systems that are use to reduce the identified risk, as well as the segment of the application where those risks exist.
- The risk for the manager is that team members leave the organisation in the middle of a project.
- For this, he can take preventive action by requesting a bond from the employee or having countable backups in the project.
12. What is the process by which states move from discovery to action?
The goal of the discovery process is to generate data that can be used to inform decisions and point to actions for remediation and quality improvement. This paper has concentrated on how to create a dependable and robust set of discovery methods to serve as the foundation for an overall quality management system. Moving from the generation of accurate and reliable data to the presentation of understandable and actionable information necessitates the use of a number of new techniques and tools.
13.Do the discovery methods generate data that informs or serves to improve the program’s policy, management, or operational aspects?
In addition to the evidence required by CMS, program managers require information in order to develop their quality management plans. As well as monitor and manage their programs. The CMS framework provides a structure for evaluating whether current discovery methods can produce information to meet this need.
14. What is the difference between the defect rejection ratio (drr) and the defect leakage ratio (dlr)?
- Firstly, DRR = Number of Defects Rejected/Tester used to evaluate tester performance
- DRR = Number of Defects Rejected/Module to evaluate module complexity
- DRR = Number of Defects Rejected/Team/Project used to evaluate team performance. and DLR = # of Defects Found/Tester DLR = # of Defects Found/Module
- DLR = Number of Defects Found/Project ( Uncovered- Defects missed out by the testing team)
15. What quality assurance and quality control activities are different for a cots / gots project than a traditional custom development project?
The activities themselves are broadly similar, but with different stakeholders and different detailed verification and validation procedures. The challenge for SQA is often determining who owns the requirements, which can be represented by a complex debate between marketing departments, technical experts, user groups, customer focus groups, and other interested parties.
16. What, in your opinion, is the role of SQA personnel in inspections and testing?
Formally, the role is to make the inspection or testing process visible to both participants (so they can see what they are accomplishing and how effective they are) and management (so that they can assess progress and risk). In practice, SQA personnel are frequently called upon to serve as facilitators or coaches. They are frequently (incorrectly) regarded as the owners or custodians of the inspection or testing process or even the owners/custodians of the entire software process.
17. What exactly is a discovery method?
A discovery method is defined as a methodical and organized activity for assessing, reviewing, evaluating, or otherwise analyzing a process, program, operation, provider, or outcome. A good discovery method produces reliable data that provides evidence to support a conclusion or action at the individual or system level.
18. Is quality control approached reactively?
Quality control is not a reactive approach; quality is built into the product from the design stage, and SPC charts indicate when the process is out of control, allowing us to take corrective action before defective products are produced.
19. What role does formal documentation play in quality management?
A quality manager can easily keep track of every process involved in the quality development of a product by creating formal documentation. They can also share this documentation with their higher-ups and stakeholders. Quality development statistics up to the present. The following are the primary advantages of formal documentation:
- Firstly, It broadens the scope of responsibility.
- Secondly, It refers to the acquisition of any process involved in quality management.
- Next, It enables an organisation and its Quality Manager to maintain consistency in the outcome.
- It enables an organisation and the Quality Manager to stay on top of the deadline.
- Further, It broadens the scope of communication within a company and among quality management teams.
- It ensures that an organization’s records are up to date.
20. Define the advantages of a Quality Management System for a company.
An organization can reap numerous benefits by adhering to a Quality Management System and effectively implementing it. Other advantages of implementing a Quality Management system include:
- It assists an organisation in increasing its efficiency in developing any product, as well as allowing the organisation to waste fewer resources.
- By implementing a Quality Management System, an organisation can maintain market consistency while also managing and controlling larger business processes.
- It enables an organisation to effectively manage various types of risks.
- A quality management system enables a company to reduce or minimise the risks of costly errors.
- It enables a company to broaden its use of the international market.
21. Explain us about the contents of your test plans and test cases.
A Quality Manager can test various aspects of a project using the contents of test plans and test cases. A Quality Manager can easily understand the requirements and weaknesses of any project by testing various aspects of it. The following items are in test plans and test cases:
- Firstly, Testing that is objective
- Examining the scope
- Next, Frame examination
- Examining the environment
- Testing the motivation for development Testing the entry and exit criteria for any process
- Testing the risk factors that may arise during the quality development cycle
22. Explain test case.
A test case can be rewritten to represent a specific condition. Checking against the Application Under Test is performed in this condition. It contains information such as test steps, prerequisites, changes in demand test environments, and other similar outputs.
23. Describe the automation test plan strategy.
The automation test plan strategy is as follows:
- Firstly, The require strategy for initiating Automation Test Strategy
- Secondly, Preparation of appropriate conditions for the Automation Test Plan
- Further, The scenario is being registered.
- Using the Error Handler Incorporation
- Script enhancements include the addition of various checkpoints and looping constructs.
- Taking the necessary steps to debug the script and resolve the issues that have arisen.
- Restarting the script execution procedure.
24. How would you distinguish between product and process quality?
Product Quality is a condition in which the Quality Manager is more concerned with finalizing the quality of a product. A Product Process, on the other hand, can be define as a procedure for establishing the necessary perimeters to manage the process involved in managing the quality of a product.
25. How would you describe Quality Auditing?
A variety of procedures are used in an organization to ensure the quality of an end product. A quality manager, on the other hand, checks each step on a regular basis in order to reduce the scope of quality-related flaws. However, even after a series of mandatory quality inspections, there is a chance that the end product’s quality will be compromised. This is why it is essential to conduct a Quality Audit. Quality auditing can be defined broadly as a systematic method of determining the efficacy of quality. It enables a Quality Manager to investigate the Quality Control procedures used to maintain and improve a product’s quality.
26. Explain how states progress from discovery to action.
The discovery process is one example of a process that is used to generate basic information. Such information can provide a Quality Manager with a decision and various points of action to improve the product’s quality. The Discovery process is more concerned with how to incorporate a set of robust methods. To progress from the state of Discovery to Action, one must abandon the production of accurate data. Furthermore, they should concentrate more on presenting a set of actionable information that necessitates the use of multiple techniques and tools.
27. How would you describe the Project Quality Management process in accordance with the PMBOK?
The Quality management process, according to the PMBOK, is made up of various quality standards. These standards can help any quality manager deliver any project or product with ease. It also provides a quality manager with steps to efficiently meet any project’s compliance.
The PMBOK Project Quality Management process consists of three major processes, which are as follows:
- Planning of high quality
- Assurance of quality
- Quality assurance
- Quality metrics are part of the quality planning process. The quality assurance process that deals with the analysis and ongoing development of production and project processes. Quality control, on the other hand, is a process that is implement in order to control the quality metrics.
28. Explain the factors that contribute to quality management results.
A quality manager is capable of bringing any result to fruition by adhering to specific motives or objectives. To achieve inefficient results, a Quality Manager should ensure that everything is done in accordance with a predetermined plan. They must pay close attention to each step or process involved in the development of any product. Furthermore, they should ensure that:
- The planned objectives are met with success.
- All initiatives have been obtained, as have the estimated standards that their enterprise had projected.
29. What are the responsibilities of a Quality Manager?
A quality manager is a professional who is in charge of inspecting a product from the time it is created until it is delivered. They have two strategies, or different types of processes, that they can use to improve the quality of an imperative. Sufficiently. It must understand how to manage the quality of any product while sustaining its resources. They must examine each and every process that will be involved in quality management. They must clearly explain the importance of quality management to their teams. While managing the quality of any product, they must keep their eyes open. They must consider each and every process that is involved in managing the product’s quality.
30. How does the Quality Manager assess his own success?
The following are the metrics that a Quality Manager should use to determine his or her success:
- It should make an effort to meet the needs of the employees. He should also be concerned with employee satisfaction.
- Next, He should always strive to raise the bar in terms of service delivery and product delivery.
- He should aim and work to achieve the given goal.
- You should always consider successfully completing any quality awareness workshop.
- Finally, here are two people who work hard enough to develop their employees individually in order to meet the demands of their customers.