Certified Supplier Quality Professional (CSQP)
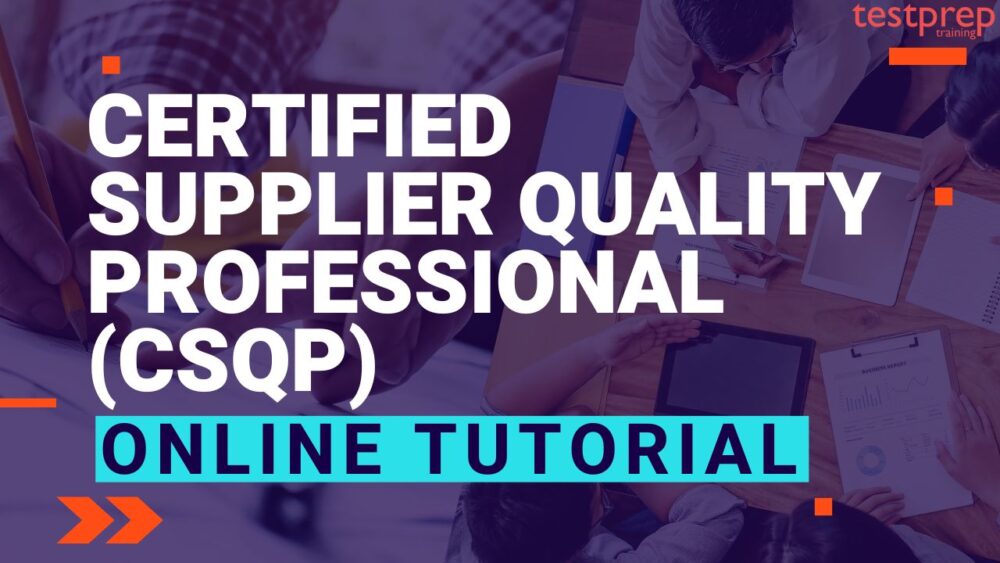
A Certified Supplier Quality Professional collaborates with an organization’s supply chain and suppliers to enhance the efficiency and longevity of essential system components by introducing process controls and crafting quality assurance strategies. This role involves monitoring performance data, pinpointing improvement opportunities, and overseeing cross-functional initiatives to boost the effectiveness of critical components and supplier partnerships.
Exam Requirements
- 8 years of on-the-job experience in areas relevant to the Certified Supplier Quality Professional Body of Knowledge.
- 3 years in a “decision-making” role, where candidates define, execute, or control projects and processes, with accountability for outcomes. This experience may or may not include managerial or supervisory duties.
- Candidates must have held a full-time, paid position.
- Prior ASQ certifications (e.g., quality engineer, quality auditor, software quality engineer, or quality manager) may satisfy some requirements, as experience used in these certifications often applies to Supplier Quality Professional certification.
Education Waivers
Candidates with completed degrees from accredited institutions may reduce the eight-year experience requirement as follows (only one waiver can be applied):
- Technical or trade school diploma — 1 year waived
- Associate degree — 2 years waived
- Bachelor’s degree — 4 years waived
- Master’s or doctorate — 5 years waived
Exam Details
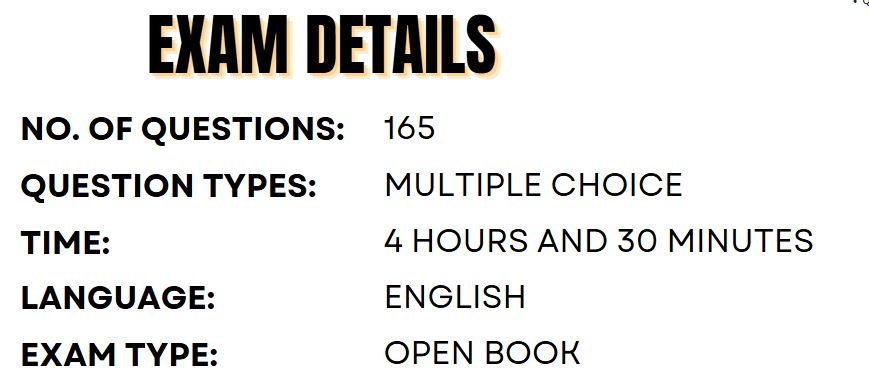
Candidates for certification must pass an exam that includes multiple-choice questions designed to assess understanding of the Body of Knowledge. The CSQP exam is a single-section test consisting of 165 questions, with a duration of four and a half hours. It is offered solely in English, with 150 questions scored and 15 unscored. For the paper-and-pencil format, the CSQP exam includes 150 questions and lasts four hours. Available translations, exam dates, and locations can be viewed here. All exams are open book, and participants are responsible for bringing their own reference materials.
Course Outline
The topics in this Body of Knowledge include detailed explanations and indicate the cognitive level at which exam questions will be designed. This information serves as a valuable resource for both the Exam Development Committee and candidates preparing for the exam. The topics include:
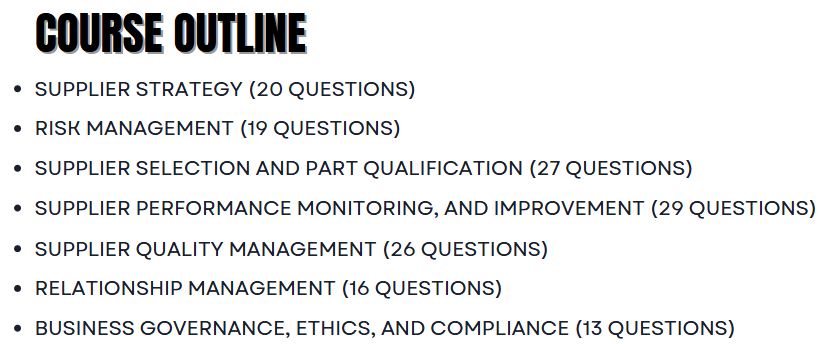
1. Supplier Strategy (20 Questions)
A. Supply Chain Vision/Mission
Assist in the development and communication of the supply chain vision/mission statement. (Apply)
B. Supplier Lifecycle Management
- Supplier Selection
- Develop the process for supplier selection and qualification, including the identification of subtier suppliers using tools such as SIPOC, decision analysis, and total risk factor analysis. (Create)
- Performance Monitoring
- Develop the supplier performance monitoring system, including expected levels of performance,
process reviews, performance evaluations, improvement plans, and exit strategies. (Create)
- Develop the supplier performance monitoring system, including expected levels of performance,
- Supplier Classification System
- Define and develop a supplier classification system (e.g., non-approved, conditionally approved,
approved, preferred, certified, partnership, and disqualified). (Create)
- Define and develop a supplier classification system (e.g., non-approved, conditionally approved,
- Partnerships and Alliances
- Identify and analyze strategies for developing customer-supplier partnerships and alliances.
(Analyze)
- Identify and analyze strategies for developing customer-supplier partnerships and alliances.
C. Supply Chain Cost Analysis
- Cost Reduction
- Identify and apply relevant inputs to prioritize cost reduction opportunities. (Analyze)
- Supply Chain Rationalization
- Interpret and analyze the optimization of a supply base to improve spending and leverage
investments into supplier quality or risk reduction. (Analyze)
- Interpret and analyze the optimization of a supply base to improve spending and leverage
- Make/Buy Decisions
- Provide input on make/buy decisions using internal and external capability analysis. Apply tools
such as SWOT analysis and use historical performance to analyze requirements. (Analyze)
- Provide input on make/buy decisions using internal and external capability analysis. Apply tools
D. Supplier Agreements or Contracts
- Terms and Conditions
- Review and provide input for developing terms and conditions that govern supplier relationships
to ensure quality considerations are addressed. (Apply)
- Review and provide input for developing terms and conditions that govern supplier relationships
- Supplier Agreements
- Identify elements of supplier agreements (e.g., business and legal approach/requirements).
(Understand)
- Identify elements of supplier agreements (e.g., business and legal approach/requirements).
- Quality Agreements
- Analyze the elements of quality agreements/requirements (e.g., other levels of approval/review). (Analyze)
- Finalization Controls
- Describe controls used to finalize terms and conditions that govern supplier relationships (e.g.,
agreements, contracts, and purchase orders). (Understand)
- Describe controls used to finalize terms and conditions that govern supplier relationships (e.g.,
E. Deployment of Strategy and Expectations
Communicate strategy internally and communicate expectations to suppliers externally. (Apply)
2. Risk Management (19 Questions)
A. Strategy
- System
- Develop a risk-based approach to manage the supply base, including business continuity,
contingency planning, and supply chain resilience. (Create)
- Develop a risk-based approach to manage the supply base, including business continuity,
- Product/Service Risk Mitigation
- Develop and implement a risk mitigation plan for predicting, minimizing, monitoring, and/or
controlling risks. (Create)
- Develop and implement a risk mitigation plan for predicting, minimizing, monitoring, and/or
- Prevention Strategies
- Identify and evaluate strategies and techniques such as supply chain mapping, avoidance,
detection, and mitigation used to prevent the introduction of counterfeit parts, materials, and
services. (Evaluate)
- Identify and evaluate strategies and techniques such as supply chain mapping, avoidance,
- Supplier Risk Identification and Categorization
- Identify supplier risks and develop categorization (e.g., organizational, business, security, and
product) using tools and models, such as the Kraljic portfolio segmentation model. (Create)
- Identify supplier risks and develop categorization (e.g., organizational, business, security, and
B. Analysis and Mitigation
- Analysis
- Identify, assess, and prioritize risks to supplier quality using tools such as decision analysis
(DA), failure mode and effects analysis (FMEA), fault tree analysis (FTA), and process auditing.
(Evaluate).
- Identify, assess, and prioritize risks to supplier quality using tools such as decision analysis
- Mitigation Control
- Develop and deploy controls such as inspection and test plans. Prioritize mitigation activities and
sustain a risk mitigation plan appropriate to the risk of the product/service. (Create)
- Develop and deploy controls such as inspection and test plans. Prioritize mitigation activities and
- Mitigation Effectiveness
- Verify the effectiveness of the control plan and improve, if necessary, using continuous
improvement methods such as plan-do-check-act (PDCA), lean, and product auditing tools.
(Create)
- Verify the effectiveness of the control plan and improve, if necessary, using continuous
3. Supplier Selection and Part Qualification (27 Questions)
A. Product/Service Requirements Definition
- Internal Design Reviews
- Identify and apply common elements of the design review process, including roles and
responsibilities of the participants. (Apply)
- Identify and apply common elements of the design review process, including roles and
- Identifying Requirements
- Identify and apply internal requirements (e.g., interrelated functional business units) for product
or service in collaboration with stakeholders, including the requirements for supply chain, subtier suppliers, and manufacturability evaluation. (Evaluate)
- Identify and apply internal requirements (e.g., interrelated functional business units) for product
B. Supplier Selection Planning
- Supplier Comparison
- Evaluate existing suppliers’ and distributors’ capabilities, capacities, past quality, delivery, price,
lead times, and responsiveness against identified requirements. (Evaluate)
- Evaluate existing suppliers’ and distributors’ capabilities, capacities, past quality, delivery, price,
- Potential Suppliers Evaluation
- Assess potential new suppliers against identified requirements using tools such as selfassessments, audits, financial analysis, and quality function deployment. Verify third-party certification status and regulatory compliance and analyze and report on results of assessments to
support the supplier selection process. (Evaluate)
- Assess potential new suppliers against identified requirements using tools such as selfassessments, audits, financial analysis, and quality function deployment. Verify third-party certification status and regulatory compliance and analyze and report on results of assessments to
- Supplier Selection
- Evaluate and select suppliers based on analysis of assessment reports and existing supplier
evaluations using decision analysis tools such as weighted decision matrices and selection
matrices. (Evaluate)
- Evaluate and select suppliers based on analysis of assessment reports and existing supplier
C. Part, Process, and Service Qualification
- Technical Review
- Interpret and evaluate technical specification requirements and characteristics such as views, title
blocks, dimensioning and tolerancing, and apply GD&T symbols as they relate to the product
and process. (Evaluate)
- Interpret and evaluate technical specification requirements and characteristics such as views, title
- Supplier Relations
- Collaborate with suppliers to define, interpret, and classify quality characteristics for the
part/process/service. (Evaluate)
- Collaborate with suppliers to define, interpret, and classify quality characteristics for the
- Process and Service Qualification Planning
- Develop a part/process/service (e.g., calibration, laboratory, software, and design) qualification
plan with supplier and internal team that includes service provider audit, calibration
requirements, sample size, first article inspection, measurement system analysis (MSA), process
flow diagram (PFD), failure mode and effects analysis (FMEA), control plans, critical to quality
(CTQ), inspection planning, capability studies, material and performance testing, appearance
approval, and internal process validation. (Analyze)
- Develop a part/process/service (e.g., calibration, laboratory, software, and design) qualification
- Part Approval
- Understand production part approval process (PPAP) requirements and ensure suppliers
understand the processes required to produce parts with consistent quality during an actual
production run at production rates. (Understand)
- Understand production part approval process (PPAP) requirements and ensure suppliers
- Validate Requirements
- Collaborate with internal team to interpret the results of the executed qualification plan for the
part/process/service, including reviewing Certificate of Compliance (CoC), Certificate of
Analysis (CoA), and production readiness reviews (PRR). (Evaluate)
- Collaborate with internal team to interpret the results of the executed qualification plan for the
4. Supplier Performance Monitoring, and Improvement (29 Questions)
A. Supplier Performance Monitoring
- Supplier Metrics
- Define, implement, and monitor supplier performance metrics such as quality, delivery (e.g., ontime delivery [OTD] and on-time in full delivery [OTIF]), cost, and responsiveness. (Evaluate)
- Supplier Performance
- Analyze supplier performance data (e.g., warranty analysis/field returns and defect rates) and
develop periodic reports (e.g., scorecard and dashboards). (Analyze)
- Analyze supplier performance data (e.g., warranty analysis/field returns and defect rates) and
- Supplier Process Performance
- Define and implement lean principles and applications such as 5S, kaizen, value stream mapping,
supplier process capabilities and controls, 8 wastes, single minute exchange of dies (SMED),
kanban, muda, standardized work, takt time, and error-proofing to reduce waste and increase
performance. (Evaluate)
- Define and implement lean principles and applications such as 5S, kaizen, value stream mapping,
B. Assess Nonconforming Product/Process/Service
- Segregate, control, and evaluate nonconforming materials to determine whether a material review board
(MRB) requires disposition. Conduct risk assessments to prevent future discrepancies. (Evaluate)
C. Supplier Corrective and Preventive Action (CAPA)
- Root Cause Analysis Tools and Methods
- Evaluate the root cause analysis of a problem using tools such as cause and effect diagrams,
Pareto analysis, 5 Why’s, fault tree analysis, design of experiments (DOE), brainstorming, check
sheets, measurement system analysis (MSA), production records, and review of process flow.
(Evaluate)
- Evaluate the root cause analysis of a problem using tools such as cause and effect diagrams,
- Collaboration with Supplier
- Evaluate and implement supplier corrective/preventive action and review its effectiveness and
robustness with supplier. Understand the process of updating failure mode and effects analysis
(FMEA) and process control plan, and understand statistical process control (SPC), 8D, and
product/process design change. (Evaluate)
- Evaluate and implement supplier corrective/preventive action and review its effectiveness and

5. Supplier Quality Management (26 Questions)
A. Supplier Quality Monitoring
- Supplier Audit
- Apply the stages of a quality audit, including audit planning, conducting the initial audit, and
executing periodic reevaluation. Understand and apply the various types of quality audits (e.g.,
product, process, and management system) and audit methods (e.g., virtual, on-site, and
desktop). (Apply)
- Apply the stages of a quality audit, including audit planning, conducting the initial audit, and
- Audit Reporting and Follow-up
- Apply and analyze audit reporting and follow up, including verification of the effectiveness of
corrective action. (Analyze)
- Apply and analyze audit reporting and follow up, including verification of the effectiveness of
- Supplier Communication
- Evaluate various communication techniques such as periodic reviews, metric and performance
indices, change management, notifications, recalls, change requests, and business updates.
Maintain active communication with suppliers to assess risk and take appropriate action.
(Evaluate)
- Evaluate various communication techniques such as periodic reviews, metric and performance
- Supplier Development and Remediation
- Identify and analyze present and future training needs and gaps, using quality methods and tools
such as kaizen and benchmarking. Use process improvement tools such as DMAIC, cycle time
reduction, defect rate, and cost reduction. Evaluate supplier remediation to develop and manage
improvement plans. (Evaluate)
- Identify and analyze present and future training needs and gaps, using quality methods and tools
- Project Management Basics
- Understand and apply various types of project reviews, such as phase-end, management, and
retrospectives or post-project reviews to assess project performance and status, to review issues
and risks, and discover and capture lessons learned from the project. Apply forecasts, resources,
schedules, and task and cost estimates to develop and monitor project plans. (Apply)
- Understand and apply various types of project reviews, such as phase-end, management, and
B. Teams and Team Processes
- Team Development
- Identify and describe the various types of teams and the classic stages of team development:
forming, storming, norming, performing, and adjourning. (Apply)
- Identify and describe the various types of teams and the classic stages of team development:
- Team Roles
- Define and describe various team roles and responsibilities for leader, facilitator, coach, and
individual member. (Understand)
- Define and describe various team roles and responsibilities for leader, facilitator, coach, and
- Performance and Evaluation
- Describe various techniques to evaluate training, including evaluation planning, feedback
surveys, pre-training testing, and post-training testing. (Understand)
- Describe various techniques to evaluate training, including evaluation planning, feedback
C. Compliance with Requirement and Supplier Categorization
- Understand and evaluate compliance with regulations and industry standards (e.g., RoHS,
Governmental regulatory authorities, and ISO), specifications, contracts, agreements, and certification
authority. Evaluate and categorize suppliers based on risk and performance. (Evaluate)
6. Relationship Management (16 Questions)
A. Supplier Onboarding
- Understand and apply processes for orientation of suppliers such as providing overview of company,
vision, mission, guiding principles, overall requirements, expectations, and criticality of product,
service, and delivery requirements. (Apply)
B. Communication
- Techniques and Mediation
- Identify and apply communication techniques (e.g., oral, written, and presentation) specifically
for internal stakeholders and suppliers to resolve issues. Apply different techniques when
working in multi-cultural environments. Identify and describe the impact that culture,
communications, and Diversity, Equity, and Inclusion (DEI) can have on an organization.
(Evaluate)
- Identify and apply communication techniques (e.g., oral, written, and presentation) specifically
- Reporting Using Quality Tools
- Use appropriate technical and managerial reporting techniques for effective presentation and
reporting, including the seven classic quality tools: Pareto charts, cause and effect diagrams,
flowcharts, control charts, check sheets, scatter diagrams, and histograms. (Analyze)
- Use appropriate technical and managerial reporting techniques for effective presentation and
C. Leadership and Collaboration
- Understand and apply techniques for coaching suppliers through regular communications, influencing without authority, negotiation techniques, conflict resolution techniques, and establish clear roles and responsibilities of internal stakeholders and suppliers using tools such as a RACI matrix (responsible, accountable, consulted, and informed). (Evaluate)
7. Business Governance, Ethics, and Compliance (13 Questions)
A. ASQ Code of Ethics
- Determine appropriate behavior in situations requiring ethical decisions, including identifying conflicts of interest, and recognizing and resolving ethical issues. (Apply)
B. Compliance and Sustainability
- Compliance
- Understand issues of compliance and their applicable policies, laws, and regulations (e.g.,
conflict of interest, confidentiality, and bribery). (Apply)
- Understand issues of compliance and their applicable policies, laws, and regulations (e.g.,
- Sustainability
- Understand and recognize the importance of environmental, social, and governance factors and
adhere to applicable sustainability policies. (Understand)
- Understand and recognize the importance of environmental, social, and governance factors and
C. Confidentiality
- Organizational Policies
- Apply organizational policies for executing appropriate agreements such as non-disclosure,
quality, and change notification agreements. (Apply)
- Apply organizational policies for executing appropriate agreements such as non-disclosure,
- Intellectual Property
- Apply procedures for protecting the intellectual property of an organization and its suppliers.
(Apply)
- Apply procedures for protecting the intellectual property of an organization and its suppliers.
- Illegal Activity
- Understand and interpret policies for reporting observations and deviations that could be
perceived as illegal activity. (Apply)
- Understand and interpret policies for reporting observations and deviations that could be
Certified Supplier Quality Professional (CSQP): FAQs
Policies and Procedures
Below are some of the exam-related policies:
Identification Policy
You must present one valid, government-issued photo ID with a signature, such as a driver’s license or passport. The name on your ID must exactly match the name on your application. During your time at the test center, all personal items will be stored in a temporary Prometric locker. You may keep only your ID and locker key with you.
References/Open Book Policy
Prometric will supply scratch paper and pencils. All ASQ exams are open books, and reference materials (including notes) must be securely bound and remain so throughout the exam. “Bound” refers to materials that are permanently bound by stitching or glue, or securely fastened in a cover by fasteners like ring binders, spiral binders, plastic snap binders, brads, or screw posts. Hand-stapled documents that are not securely fastened are not permitted. The Test Center Administrator (TCA) will review all reference materials before you enter the exam room. “Post-It” notes may be used as tabs, but they must be attached before entering the test center.
Certified Supplier Quality Professional (CSQP) Exam Study Guide
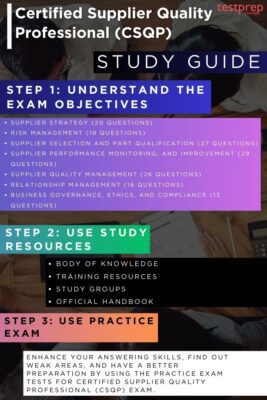
1. Understand the Exam Body of Knowledge
The Body of Knowledge (BOK) is an essential tool for candidates preparing for the Certified Supplier Quality Professional (CSQP) exam. It outlines key topics and includes additional details, such as subtext explanations and cognitive levels, which provide valuable insights into the specific content that may appear on the test. By using the BOK, candidates can focus their studies on areas most relevant to the exam, understanding how each topic applies to the role of a supplier quality professional.
The subtext serves as a guide rather than a limitation, offering clarity on core concepts without restricting the scope of potential questions. Each topic’s cognitive level descriptor also helps candidates gauge the depth of knowledge required, with a comprehensive breakdown of these levels available for further guidance.
2. Use the ASQ CSQP Exam Official Handbook
The ASQ Certified Supplier Quality Professional Handbook, Second Edition provides a comprehensive guide for professionals dedicated to creating a safe, efficient, cost-effective, and high-quality supply chain. Through this handbook, readers can learn strategies for collaborating with key suppliers to enhance performance by applying process controls and establishing quality assurance frameworks. It serves both as an in-depth study resource for candidates preparing for the ASQ Certified Supplier Quality Professional (CSQP) exam and as an updated reference for active professionals. This revised edition covers:
- A complete review of the 2023 ASQ CSQP Body of Knowledge (BoK).
- New topics, including supplier and quality agreements, finalization controls, supplier risk identification and classification, and sustainability.
- Practical tools like conflict resolution methods, weighted decision-making matrices, total risk factor analysis, and the RACI matrix.
3. CSQP Exam Training
Utilize this virtual training to explore the seven core domains of the Certified Supplier Quality Professional (CSQP) Body of Knowledge (BoK) in preparation for certification. Guided by seasoned instructors, you’ll gain insights through practical examples and case studies covering the development and management of quality control systems, the application and analysis of testing and inspection methods, the use of metrology and statistical techniques to resolve quality issues, an understanding of human factors and motivation, quality cost principles, and methodologies, as well as the skills to establish management information systems and audit quality systems to identify and address deficiencies.
ASQ also provides this training in an in-person format, with on-site options available for groups of five or more, delivering convenience, cost-efficiency, and potential course customization when you bring ASQ’s expert instructors directly to your organization.
4. Join Study Groups
Joining study groups can be a valuable asset for those preparing for the Certified Supplier Quality Professional (CSQP) exam. Study groups provide a collaborative environment where candidates can share knowledge, discuss complex topics, and clarify challenging concepts within the CSQP Body of Knowledge. Group members can benefit from diverse perspectives, test each other’s understanding, and exchange resources like study materials and practice questions. Study groups also help in staying motivated and accountable, fostering a structured approach to exam preparation. By learning from peers who may have hands-on experience in different aspects of supplier quality, candidates can enhance their readiness and confidence for the CSQP exam.
5. Take Practice Tests
Taking practice tests is an essential strategy for effective preparation for the Certified Supplier Quality Professional (CSQP) exam. These tests simulate the actual exam environment, allowing candidates to familiarize themselves with the format, question types, and time constraints they will encounter on exam day. By assessing their knowledge across the CSQP Body of Knowledge, candidates can identify strengths and pinpoint areas needing improvement. Regularly completing practice tests helps reinforce learning, boosts confidence, and enhances test-taking skills. Additionally, reviewing the results of practice tests provides valuable insights into which topics require further study, ultimately leading to a more targeted and efficient preparation process for the CSQP exam.
