CIPS Level 3 Advanced Certificate in Procurement and Supply Operations Interview Questions
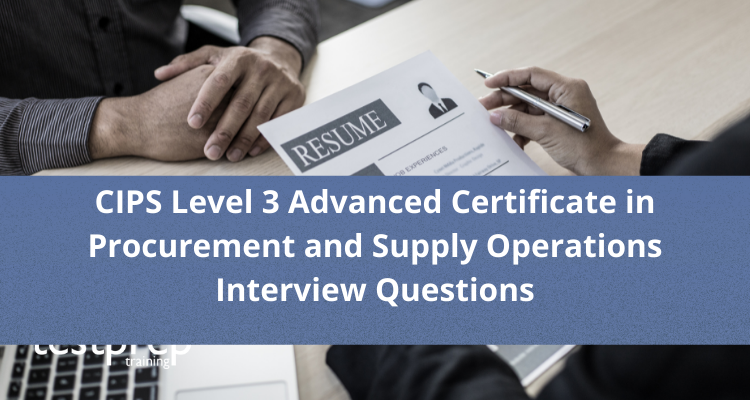
The CIPS Level 3 Advanced Certificate in Procurement and Supply Operations Exam is a global certification that assists candidates in developing industry-standard skills needed to launch a career in procurement and supply. This is one of five certifications offered by the Chartered Institute of Procurement and Supply, and the second of three entry-level qualifications (CIPS). It is an entry-level qualification that focuses on the theory, processes, and skills of procurement and supply. This also teaches how to deal with a variety of difficult tasks at work. An industry-standard qualification demonstrates to employers that the candidate adheres to the highest professional standards, has up-to-date skills, and can apply their expertise across the private, public, and non-profit sectors. Therefore, to help you prepare for CIPS Level 3 Advanced Certificate in Procurement and Supply Operations Interview we have curated expert level questions and answers:
Advanced Interview Questions
What is the role of procurement and supply operations in an organization?
The role of procurement and supply operations is to manage the process of purchasing goods, services and works needed by an organization. This includes activities such as:
- Identifying requirements: Determine what the organization needs and when it is needed.
- Sourcing: Identifying and evaluating potential suppliers and negotiating contracts.
- Procurement: Conducting the process of purchasing goods, services, and works.
- Supply chain management: Ensuring the timely delivery of goods and services and managing the flow of materials, information, and payments.
- Contract management: Monitoring supplier performance, resolving disputes, and ensuring that the terms of the contract are met.
- Cost management: Ensuring that procurement processes are cost-effective and that the organization is getting value for money.
The ultimate goal of procurement and supply operations is to ensure that the organization has the resources it needs, when it needs them, at a reasonable cost.
What are the main differences between purchasing and procurement?
Purchasing and procurement are related but different concepts in supply chain management. Purchasing refers to the process of buying goods or services to meet an organization’s needs. Procurement, on the other hand, encompasses all the activities involved in acquiring goods and services, including strategic sourcing, negotiating, and managing contracts. It is a broader term that includes purchasing as a subset
- Definition: Purchasing refers to the act of buying goods or services for a company. Procurement, on the other hand, refers to the process of acquiring goods, services or works from an external source, through a process that includes planning, specifying, selecting, and contracting for the delivery and management of products, services, and/or works.
- Focus: Purchasing focuses mainly on the buying process and acquiring goods or services. Procurement takes a broader approach that includes sourcing, negotiation, and supplier management.
- Scope: Purchasing is typically limited to the transaction and delivery of goods or services. Procurement encompasses all the stages of the sourcing process, from identifying needs to evaluating and selecting suppliers, negotiating contracts, and managing the relationship with the supplier.
- Responsibility: Purchasing is primarily the responsibility of the buyer, while procurement is a cross-functional process that involves many stakeholders, including purchasing, finance, legal, and supply chain management.
- Objectives: The primary objective of purchasing is to purchase goods or services at the lowest possible cost, while the objective of procurement is to ensure that the right goods, services, or works are procured at the right time, at the right price, and from the right source, with the aim of improving overall value for the organization.
- Strategic Importance: Purchasing is considered a tactical function, while procurement is considered a strategic function that can have a significant impact on the company’s bottom line.
Could you explain the difference between strategic procurement and operational procurement?
Strategic procurement and operational procurement are two different approaches to procurement management, with different objectives, processes, and focus areas.
- Strategic procurement: Involves a long-term, company-wide approach to procurement that aligns procurement activities with organizational goals and objectives. It is focused on developing supplier relationships, reducing costs, improving quality and innovation, and increasing competitiveness. Strategic procurement involves the development of procurement strategies, policies, and plans that support the organization’s overall objectives.
- Operational procurement: Involves the day-to-day procurement activities that support the delivery of specific projects and programs. It is focused on the procurement of goods, services, and works required to deliver specific projects and programs. Operational procurement is concerned with the efficient and effective procurement of goods, services and works, ensuring that procurement activities are completed on time, within budget, and to required quality standards.
In summary, strategic procurement focuses on long-term goals and aligning procurement with the organization’s objectives, while operational procurement focuses on the day-to-day procurement activities required to support project delivery.
Can you explain the stages of the procurement cycle?
The procurement cycle refers to the series of steps or stages that organizations go through to acquire goods, services, or works. The stages of the procurement cycle are:
- Requirements definition: Determining the need for goods, services, or works and defining the specific requirements for each.
- Sourcing: Identifying potential suppliers and conducting market research to determine the best options.
- Tendering: Inviting potential suppliers to submit bids or proposals for the goods, services, or works required.
- Evaluation: Analyzing the bids or proposals received to determine the best option based on criteria such as quality, price, and delivery times.
- Contract award: Selecting the supplier and awarding the contract.
- Contract management: Monitoring supplier performance and ensuring that the terms of the contract are being met.
- Closure: Finalizing the procurement process and closing the contract.
How do you determine the best suppliers to work with?
To determine the best suppliers to work with in procurement and supply operations, you can follow these steps:
- Define your requirements: Clearly define the goods, services, or works required and the criteria that are important to you, such as price, quality, delivery time, and sustainability.
- Conduct market research: Research the market to identify potential suppliers and gather information about their capabilities, experience, and reputation.
- Evaluate suppliers: Compare potential suppliers against the criteria you have defined and eliminate those that do not meet your requirements.
- Select a shortlist of suppliers: From the remaining suppliers, select a shortlist of suppliers that best meet your requirements.
- Conduct supplier assessments: Assess the shortlisted suppliers in more detail to determine which suppliers are the best fit for your organization. This can include site visits, reference checks, and financial assessments.
- Negotiate with suppliers: Once you have selected your preferred suppliers, negotiate terms and conditions with each supplier to ensure that both parties are satisfied with the agreement.
- Continuously monitor supplier performance: Continuously monitor supplier performance to ensure that they continue to meet your requirements and make any necessary adjustments to the agreement.
By following these steps, you can determine the best suppliers to work with in procurement and supply operations, ensuring that you receive the goods, services or works you need at a competitive price and to the required quality standards.
Can you provide an example of a procurement negotiation and how it was successfully resolved?
I was recently involved in a procurement negotiation for my company. The goal was to purchase raw materials from a supplier at a competitive price. The supplier had a reputation for providing high-quality products but their prices were usually on the higher side. I was tasked with negotiating a better price for my company.
The negotiation was challenging as the supplier was not willing to budge on their price. However, I was determined to reach a mutually beneficial agreement. I started by highlighting the long-term partnership my company had with them and the value we placed on the quality of their products. I then presented a competitive offer that was lower than their asking price but still within their profit margins.
The supplier was hesitant at first, but I explained that the lower price would allow my company to place larger orders and increase their business in the long run. I also offered to sign a long-term contract with them to further secure their business.
The supplier agreed to our offer and the negotiation was successfully resolved. This resulted in a win-win scenario for both parties. My company was able to secure the raw materials at a competitive price and the supplier was able to secure a long-term contract and increased business.
In conclusion, effective communication, mutual respect, and a willingness to compromise were key factors in successfully resolving the procurement negotiation.
What is supplier relationship management and how does it impact the procurement process?
Supplier relationship management (SRM) is the process of managing and optimizing interactions with suppliers to maximize value and minimize risk. It involves developing and maintaining a long-term, collaborative relationship with key suppliers to ensure that they can meet the organization’s needs and objectives.
SRM has a significant impact on the procurement process as it helps organizations to:
- Improve supplier performance: By working closely with suppliers, organizations can identify areas for improvement and implement changes to increase supplier performance and reliability.
- Enhance supplier collaboration: SRM promotes collaboration between the organization and its suppliers, resulting in better communication, problem resolution, and information sharing.
- Reduce costs: By developing a close relationship with suppliers, organizations can negotiate better terms and prices, and reduce the costs of goods and services.
- Minimize risk: By having a good relationship with suppliers, organizations can reduce the risk of supply chain disruptions, price increases, and other supply-related issues.
In conclusion, effective supplier relationship management is a critical component of the procurement process, as it helps organizations to improve supplier performance, reduce costs, and minimize risk.
How do ethical and sustainable procurement practices benefit an organization?
Ethical and sustainable procurement practices can bring numerous benefits to an organization. Here are a few:
- Reputation and Brand Image: Adopting ethical and sustainable procurement practices can help an organization build a positive reputation and enhance its brand image. Customers and stakeholders are increasingly seeking companies that prioritize ethical and sustainable business practices, and a commitment to ethical procurement can help organizations stand out from their competitors.
- Cost savings: Sustainable procurement can lead to cost savings in the long run. For example, buying products that are environmentally friendly or made from sustainable materials can reduce the organization’s carbon footprint and save money on energy costs.
- Improved Supply Chain Management: Ethical and sustainable procurement practices can help organizations better manage their supply chains, reducing the risk of supply chain disruptions and increasing the resilience of the organization.
- Employee Engagement and Loyalty: Employees are increasingly seeking employers that prioritize ethical and sustainable business practices. Adopting ethical procurement practices can help organizations attract and retain top talent, improving employee engagement and loyalty.
- Better Compliance with Regulations: Many countries have regulations in place to encourage sustainable and ethical business practices. Adopting ethical procurement practices can help organizations comply with these regulations, reducing the risk of legal or financial penalties.
Overall, ethical and sustainable procurement practices can bring numerous benefits to an organization, including a better reputation, cost savings, improved supply chain management, increased employee engagement and loyalty, and better compliance with regulations.
Can you describe a complex procurement project you have worked on and the challenges you faced?
I worked on a complex procurement project for a large multinational corporation. The project involved the procurement of various IT equipment, software, and services for multiple locations across the globe. The main challenge was to ensure that all procurement was done within the budget, while still meeting the specifications and quality requirements of the company.
One of the biggest challenges I faced was coordinating with the stakeholders across different countries and time zones. Each location had its own set of requirements, and it was difficult to ensure that everyone was on the same page and that all procurement was done in a timely and efficient manner. Additionally, there were different regulations and laws in each country, which made it difficult to ensure that all procurement was done in accordance with local laws and regulations.
Another challenge I faced was ensuring that the procurement was done in a way that was transparent and fair. This was especially important in light of the large sums of money involved in the procurement. To ensure that the procurement was done in a fair and transparent manner, I worked closely with the procurement team, legal team, and finance team to ensure that all procurement was done in accordance with the company’s policies and procedures.
Despite the challenges, I was able to successfully complete the procurement project. The company was able to acquire all the IT equipment, software, and services it needed within the budget, and all procurement was done in accordance with the company’s policies and procedures.
What do you think is the future of procurement and supply chain management?
Based on trends and developments, the future of procurement and supply chain management is likely to be characterized by greater automation and digitization, increased collaboration and supply chain visibility, and a stronger focus on sustainability and responsible sourcing.
The use of technology, such as artificial intelligence and blockchain, is expected to streamline procurement processes and provide organizations with real-time data and insights into their supply chains. This will enable organizations to make more informed decisions, reduce costs, and improve supplier performance.
Additionally, the increasing importance of sustainability and responsible sourcing is likely to drive changes in procurement and supply chain practices, as organizations seek to reduce their environmental impact and ensure that their suppliers adhere to ethical standards.
Overall, the future of procurement and supply chain management is expected to be shaped by the need to increase efficiency, reduce costs, and minimize risks, while also addressing sustainability and social responsibility concerns.
Basic Interview Questions
1. Define Supply Operations.
The systems, structures, and processes use to plan and execute the flow of goods and services from supplier to customer are referred to as supply chain operations. It is critical to evaluate both internal operations and the extended supply chain, which includes suppliers and customers, in order to maximize effectiveness.
2. What is the overarching goal of Supply Operations?
The goal of supply operations is to maximize productivity and efficiency in an organization’s operations. Companies hope to satisfy people’s demands by delivering the right goods to them on time while profiting from the process.
While streamlining the entire process, supply chain managers ensure that waste is minimise and that everyone’s time is used productively, allowing the organization to save money. All of these smaller objectives lead to the ultimate goal of achieving efficiency.
3. What exactly do you mean by affreightment?
The term affreightment is derive from the word freight. It is the sum of money paid to a charterer in exchange for renting his vessel to transport the goods.
4. What all components are there in supply operations?
Without collaborative and integrative practices with channel partners, supply chain management is incomplete. A supply chain operation’s success is dependent on suppliers, retailers, wholesalers, distributors, and customers. Supply chain managers must collaborate with suppliers, monitor demand, integrate wholesaler and distributor services, and effectively communicate with everyone involved in the process, including customers.
5. How do you define SKU keeping the supply chain in mind?
SKU is an abbreviation for stock-keeping units. It has something to do with inventory management. The term SKU refers to a specific item stored in a specific location in the inventory.
6. How do you define compliance labels?
A product compliance label is created with careful consideration for the standardized procedures of the industry associated with the product. It is important in import/export because it is up to government agencies to define and check these label requirements for exported or imported products.
7. What is logistics’ role in supply chain management?
“Logistics” refers to the entire process of monitoring the transport of goods and services from one location to their intended destination. Originally, the term logistics referred to the transportation of equipment to military armies on the ground. However, in modern times, logistics is more than just a definition. It can easily shapeshift to meet the needs of an organization. It entails more than just delivering finished goods to customers.
8. What’s the distinction between supply chain management and logistics?
Logistics and supply chain management are two very different processes. While supply chain management is concerned with the big picture, logistics is concerned with the details. Logistics is the process of producing goods in one organization and distributing them to consumers who require the goods. Supply chain management, on the other hand, refers to a group of organizations that work together to distribute goods in large quantities to their customers.
9. What is the role of logistics?
Logistics is important because if consumers do not receive their desired goods, the entire point of production is rendered null and void. Logistics may appear to be a minor process that occurs at the end, but it bears the weight of the entire manufacturing process. When the goods are manufactured and ready to ship, logistics does not come into play. It is an ongoing process that occurs throughout the manufacturing process. In fact, logistics begins even before the production process begins. Logistics plays a role in the raw material procurement process.
10. What activities are performed in logistics?
Logistics operations can be divided into three broad categories. This includes receiving goods from suppliers, warehousing them, and delivering them to the intended consumers. That, however, is a very broad definition of everything that happens at the operational level of logistics. To begin, the require resources are obtained from the supplier and packaged for transport. This can be accomplished by air, sea, or road. When the goods arrive at their destination, they are cleared through customs and deliver to the warehouse where they will be store. These goods are check for quality and grouped accordingly while in storage. The inventory’s details are scrutinize for any discrepancies.
11. Specify the Advance Shipping Notice.
It is delivered to the customer prior to the delivery. Next, it contains all of the information about their product shipment. It includes information about the shipment’s carrier, when the shipment can be expected, and so on.
12. What exactly do you mean by anti-dumping duty?
It is an import duty levied when the charges of imported goods are lower than the determined price in the exporter’s country’s market. This causes deficits in the importing country’s domestic market.
13. Can you explain the phrase “less than a truckload”?
“Less than truckload” refers to a contract between the transport owner and the shipper in which the owner is not paid in full for the truck. Next, the cost of the shipment is calculated base on the weight of the goods and the distance traveled.
14. What is the definition of Dead Weight Tonnage?
The difference between a ship’s laden and unladen weight is referred to as deadweight tonnage. This means that the weight of all items on the ship is taken into account, except for the ship’s weight.
15. What are the main supply chain challenges that businesses are currently facing?
The supply chain is a vast and fruitful field that offers numerous opportunities for exploration and experimentation. Companies that do not invest in supply chain management pay a high price in today’s competitive market.
Many critical factors are overlooked by these businesses, including:
- Firstly, costs are rising throughout the supply chain.
- Secondly, consumers want faster delivery and higher levels of customer satisfaction.
- Also, market volatility, for example, is a source of volatility in the supply chain.
16. What are the safety considerations to be made during warehouse transportation?
Warehouse transportation is not the safest method available. It carries its own set of risks. One must always be cautious enough to avoid them.
- Firstly, sharp objects must be remove as soon as possible.
- Secondly, any loose flooring or areas that could cause tripping should be addressed.
- Next, fire exits must be operational.
- Further, the proper use of garbage cans should be promote.
- Next, items should be place in their proper locations.
17. What exactly is a blanket way bill?
A Blanket Way Bill is one that contains two or more consignments of freight.
18. What are the main problems that transportation encounters during warehousing?
The warehousing process is not as simple as we believe. It has tracking and communication issues. The safety of a warehouse is a major deciding factor when storing goods. Any delays are account for, and the costs incurred are occasionally troubling.
19. Are you able to tell the difference between direct and indirect distribution channels?
- Firstly, direct distribution channels are those that do not involve any intermediaries. Small businesses benefit greatly from direct distribution channels.
- Secondly, indirect distribution channels rely on wholesalers and are best to large-scale productions. They also raise costs by putting vendors and external channel partners between the business and the consumer.
20. Could you please explain the significance of compliance labels in a nutshell?
Compliance labels are regulatory guidelines establish by a customer, stakeholder, industry, or government. They are useful in supply chain management because they eliminate inconsistency in manufacturing. Compliance labels are especially important for businesses looking to expand into new markets.
21. Describe the use of SKU for inventory.
SKU is an abbreviation for storage keeping units. It’s a scannable bar code that vendors can use to track inventory transportation and levels digitally. If the inventory level falls below a certain level, the SKU code may issue a warning.
22. What exactly is anti-dumping duty?
Anti-dumping duty is an import duty levied when imported goods are price lower than the normal price in the exporter’s domestic market and cause material loss to the importing country’s domestic industry.
23. What is the definition of deadweight tonnage?
The difference between the ship’s laden and unladen weight is referred to as deadweight tonnage. In other words, it is the weight of everything except the ship itself that the ship carries.
24. What exactly is cross docking?
Cross-docking is the process of unloading materials from incoming semi-trucks and loading them directly into outgoing trucks or trailers. It lowers handling costs, operating costs, and inventory storage costs.
25. What is the declared value for carriage?
The declared value for carriage is the value of the goods declare by the shipper on the bill of lading in order to determine the carrier’s liability limit or a freight rate.
26. What exactly is documents against acceptance?
A document against acceptance arrangement or provision is one in which the exporter instructs a bank to hand over shipping and title documents to the importer only if the importer signs the accompanying bill of exchange or draught. Further, this clause ensures that the buyer is legally obligate to pay the full price for the shipments to the exporter before ownership is transfer.
27. What do you understand by carton clamps?
It is the most adaptable attachment for handling and transporting a variety of unpalletized products such as furniture, cartons, appliances, and so on.
28. Define Compliance Labels.
Compliance labels are commonly use as shipping labels, carton labels, and pallet labels, and they typically include bar codes. It is use to identify the goods that have been delivering.
29. What do you understand by Consignment Inventory?
Consignment inventory is in the customer’s possession but is still own by the supplier. That is, you will only pay the supplier when their goods are sold.
30. Explain Chargeback.
When a shipment fails to meet the customer’s agreed-upon terms and conditions, the customer imposes a financial penalty on the supplier. This is chargeback. For instance, improper packaging or labeling.
Conclusion for CIPS Level 3 Advanced Certificate in Procurement and Supply Operations Interview
Jobs in Procurement and Supply Operations can be found all over the country and around the world. As a result, you can select job profiles both locally and regionally within the country. And, if you enjoy traveling, many supply chain management positions require you to travel both nationally and internationally on a regular basis. Also, as more businesses realize the true value of a well-articulated CIPS Level 3 Advanced Certificate in Procurement and Supply Operations management system, the demand for skilled and certified Procurement and Supply Operations professionals will rise.